
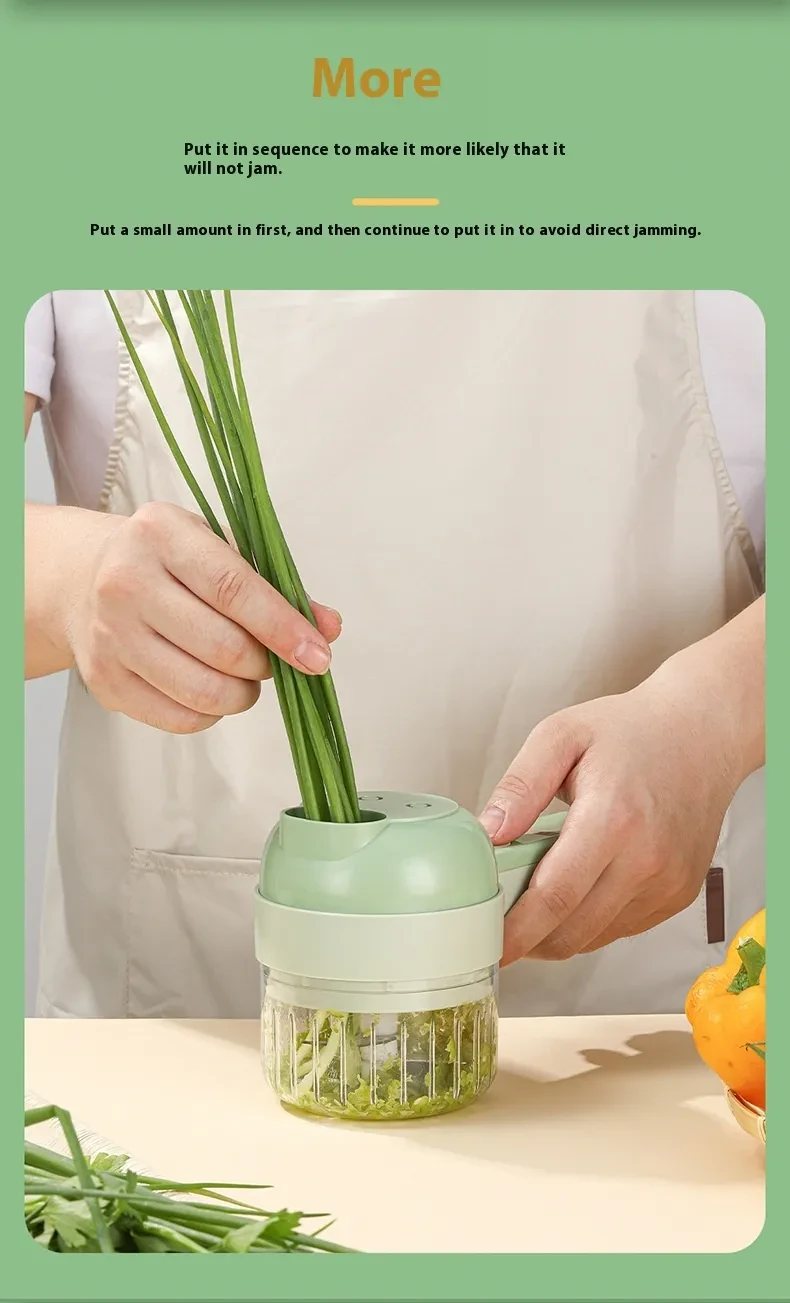
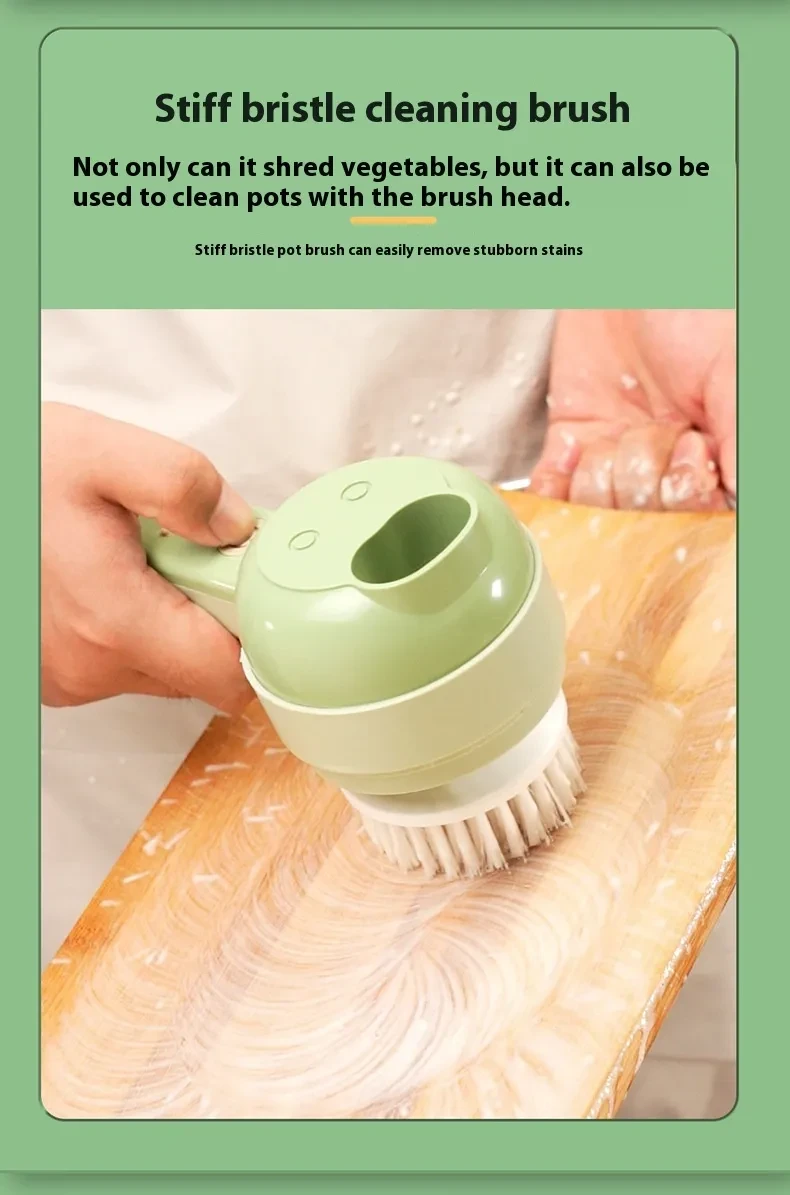
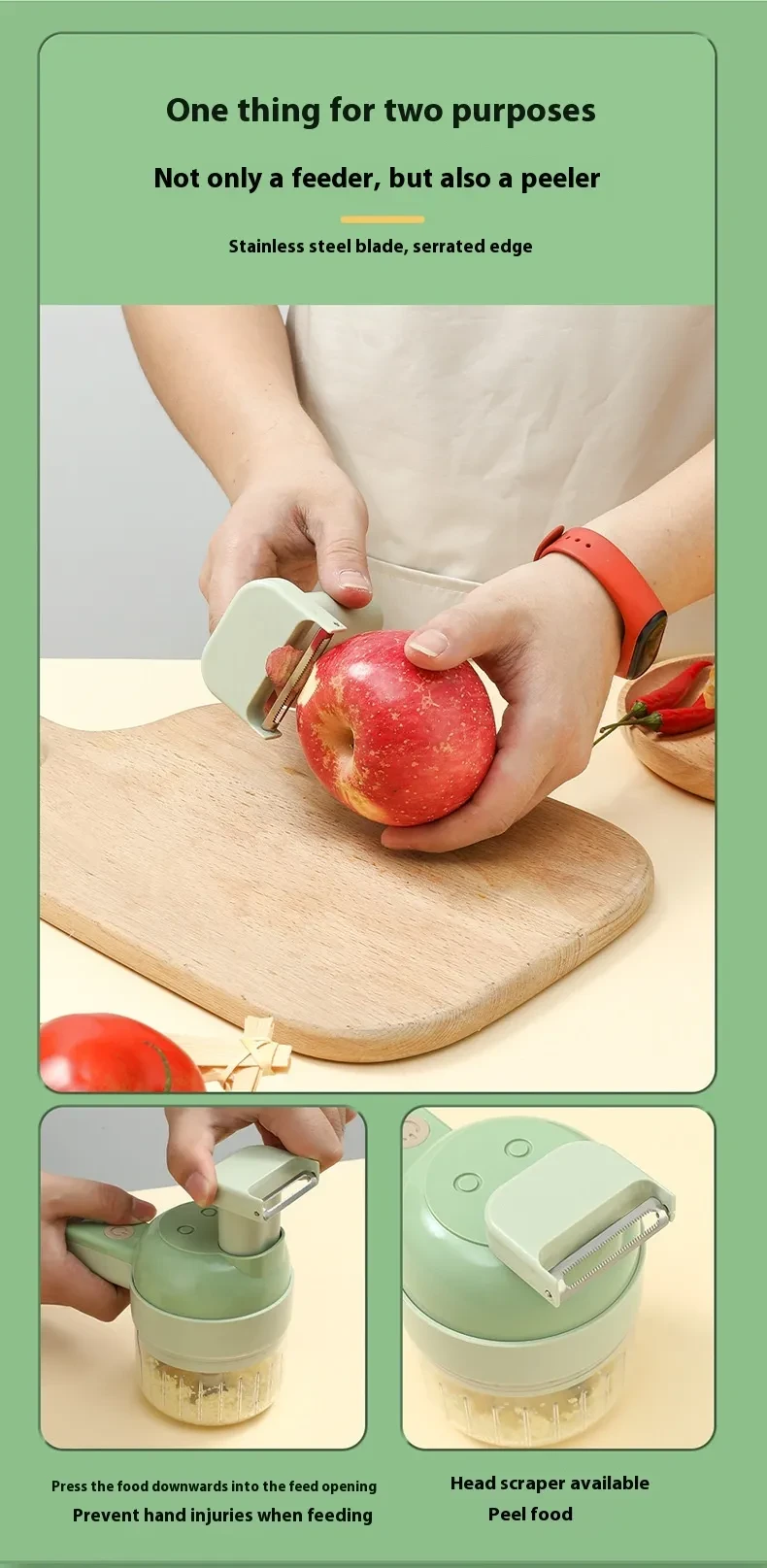
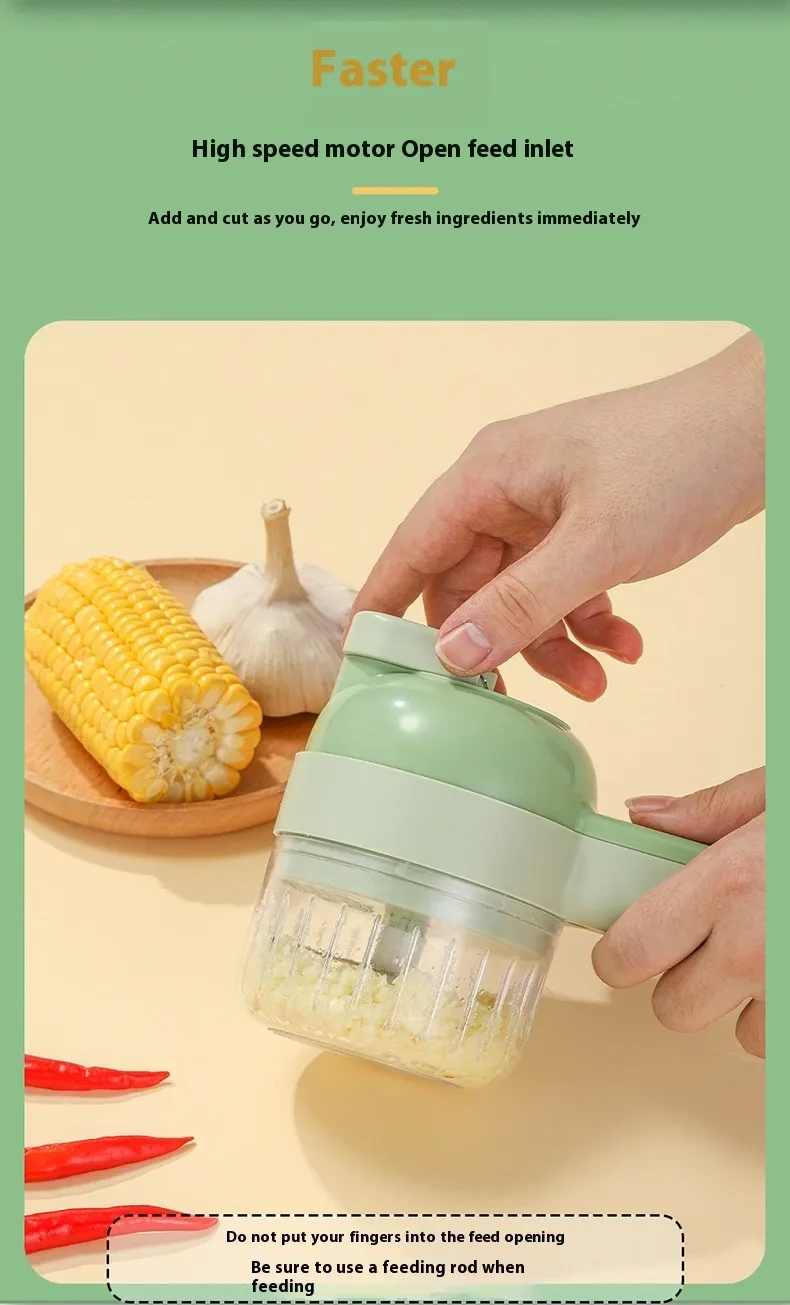
Plastic Processing Machine
Approx $59.13 USD
Plastic Processing Machine: Revolutionizing the Manufacturing Industry
The Plastic Processing Machine is a pivotal tool in the manufacturing and recycling sectors, designed to transform raw plastic materials into useful products or components through various mechanical processes. These machines play a crucial role in industries ranging from automotive to packaging and consumer goods. With advanced features and technological innovations, modern plastic processing machines offer enhanced precision, efficiency, and flexibility, making them indispensable in today’s fast-paced production environments.
What is a Plastic Processing Machine?
A Plastic Processing Machine is an industrial device used to mold, shape, or recycle plastic materials into finished products or components. These machines use a variety of methods, such as injection molding, extrusion, blow molding, and thermoforming, depending on the type of plastic product being produced. They are designed to handle different forms of plastic, including thermoplastics and thermosets, allowing manufacturers to create a wide range of products for various industries.Plastic processing machines are found in many factories and production lines, where they help streamline the manufacturing process by providing consistent, high-quality outputs while reducing labor costs and material waste.
Types of Plastic Processing Machines
1. Injection Molding Machines
Injection molding is one of the most popular methods for manufacturing plastic parts. In this process, melted plastic is injected into a mold under high pressure to form the desired shape. Injection molding machines are used to produce products ranging from consumer electronics, automotive components, medical devices, and even everyday items like bottles and toys. These machines offer high precision and are ideal for mass production of complex shapes.
- Key Features: High precision, high speed, excellent for large-scale production, and capable of producing intricate designs.
2. Extrusion Machines
Extrusion machines are used to mold plastic materials into continuous shapes, such as pipes, films, sheets, and profiled products. The process involves forcing heated plastic through a mold or die, creating long sections of material that can be cut into specific lengths. Extruders are commonly used in the production of plastic films for packaging, pipes for plumbing, and various other everyday products like window frames.
- Key Features: Suitable for continuous production, high-volume output, and cost-effective for producing long shapes.
3. Blow Molding Machines
Blow molding is the method used to produce hollow plastic products, such as bottles, containers, and tanks. The process involves inflating a tube of melted plastic into a mold, forming the desired shape. Blow molding machines are extensively used in the production of packaging materials, especially for liquid products.
- Key Features: Ideal for producing hollow items, such as plastic bottles, and containers, with high-speed output and versatility in product design.
4. Thermoforming Machines
Thermoforming machines are used to heat plastic sheets until they become pliable and then mold them over a mold to create the desired shape. After cooling, the molded plastic retains its shape. These machines are used to make plastic trays, blister packs, plastic lids, and more. Thermoforming is often used for packaging, medical products, and food containers.
- Key Features: Cost-effective for medium-to-high volume production, easy to mold a variety of shapes, and commonly used in the packaging industry.
5. Rotational Molding Machines
Rotational molding is a technique used to produce large hollow plastic parts, such as storage tanks, toys, and playground equipment. The plastic is placed inside a mold, which rotates in multiple axes to evenly coat the mold with the melted plastic, resulting in a consistent and uniform product.
- Key Features: Excellent for producing large and hollow plastic items, capable of creating complex shapes, and ideal for low- to medium-volume production.
Key Features of Plastic Processing Machines
1. Advanced Control Systems
Modern plastic processing machines come equipped with advanced control systems that allow operators to monitor and adjust various parameters, such as temperature, pressure, speed, and timing. These systems enable precise control over the production process, ensuring that products meet the desired specifications.
2. Energy Efficiency
With growing concerns over energy consumption and environmental impact, many plastic processing machines are now designed with energy efficiency in mind. These machines incorporate features like low-energy motors, optimized heating systems, and automated shut-off functions to reduce power consumption during production, making them more eco-friendly and cost-effective in the long run.
3. High Precision and Consistency
Plastic processing machines, particularly injection molding and extrusion machines, are capable of achieving high levels of precision in product design and dimensions. This ensures consistency across large production runs, which is crucial for industries that require uniformity in their products, such as in the medical, automotive, and consumer electronics sectors.
4. Automation and Integration
Many modern plastic processing machines are equipped with automated features that enhance production efficiency. Automated robotic arms can handle tasks such as loading materials, removing finished products, and packaging. Additionally, these machines can be integrated with other equipment in the production line for seamless operation, reducing manual labor and increasing output.
5. Versatility and Customization
Plastic processing machines are highly versatile, capable of processing a wide range of plastic materials such as polyethylene, polypropylene, PVC, ABS, and more. These machines can be customized to suit the specific needs of a particular production process or industry, enabling manufacturers to produce a broad array of products in various shapes and sizes.
Benefits of Using a Plastic Processing Machine
1. Increased Efficiency and Productivity
By automating the production process, plastic processing machines significantly increase efficiency and productivity. They can produce large quantities of plastic products in a fraction of the time it would take using manual methods, reducing overall production costs.
2. Reduced Waste
Plastic processing machines, particularly injection molding and extrusion machines, are highly precise, reducing material waste during production. This helps businesses save costs by maximizing the use of raw materials and minimizing scrap rates.
3. High-Quality Products
With their ability to produce products with consistent dimensions, plastic processing machines ensure that the final product meets high-quality standards. This is especially important for industries like automotive and medical devices, where product quality and precision are critical.
4. Customization of Products
Plastic processing machines allow manufacturers to easily customize products according to design specifications. Whether it’s the thickness of a plastic sheet, the shape of a plastic component, or the color of a finished product, these machines offer flexibility and precision in product creation.
5. Cost-Effective Production
Although plastic processing machines require an initial investment, they quickly pay for themselves through increased productivity, reduced labor costs, and lower material waste. This makes them a cost-effective solution for mass production of plastic products.
Applications of Plastic Processing Machines
Plastic processing machines are used in a wide range of industries, including:
- Packaging: For producing containers, bottles, and films.
- Automotive: For manufacturing interior and exterior parts like dashboards, bumpers, and trim components.
- Medical Devices: For producing precision parts and devices like syringes, IV components, and diagnostic equipment.
- Consumer Goods: For creating everyday items like toys, kitchenware, and home appliances.
- Construction: For producing pipes, panels, and insulation materials.
Product information:
Style: Modern and minimalist
Function: electric, automatic, multifunctional
Material: ABS
Size: approximately 20.5 * 9.5 * 8cm
Packing list:
Cooking kit * 1
C port charging wire * 1
Slicing kit * 1
Material shovel * 1
Cleaning brush * 1
Infeed device * 1
Garlic mixer * 1
The product may be provided by a different brand of comparable quality.
The actual product may vary slightly from the image shown.