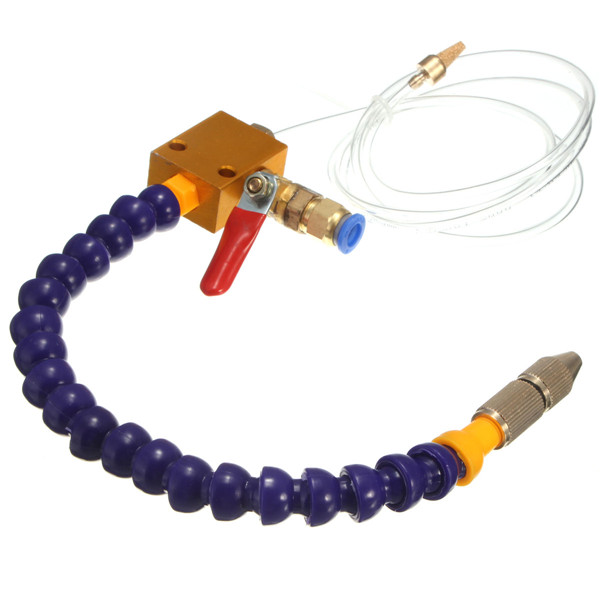
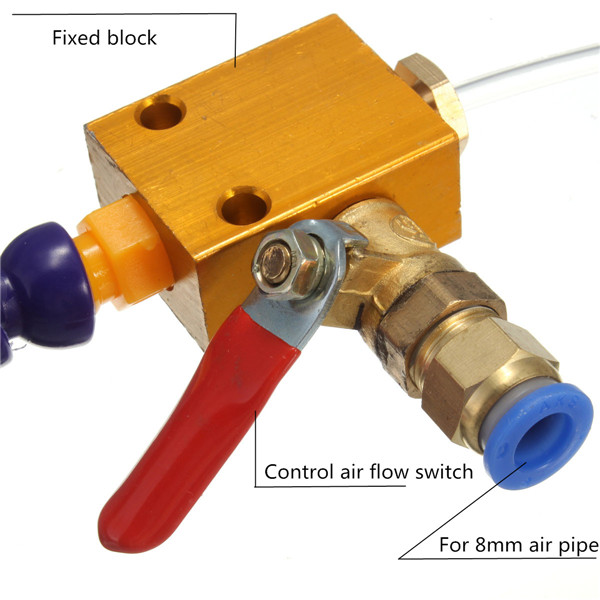
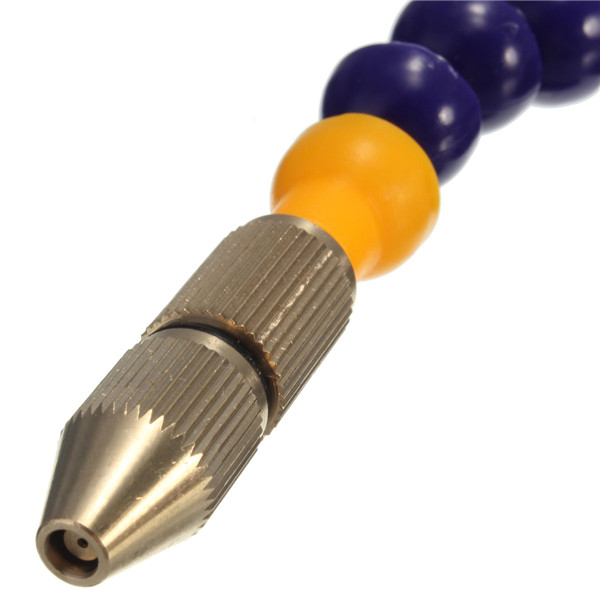
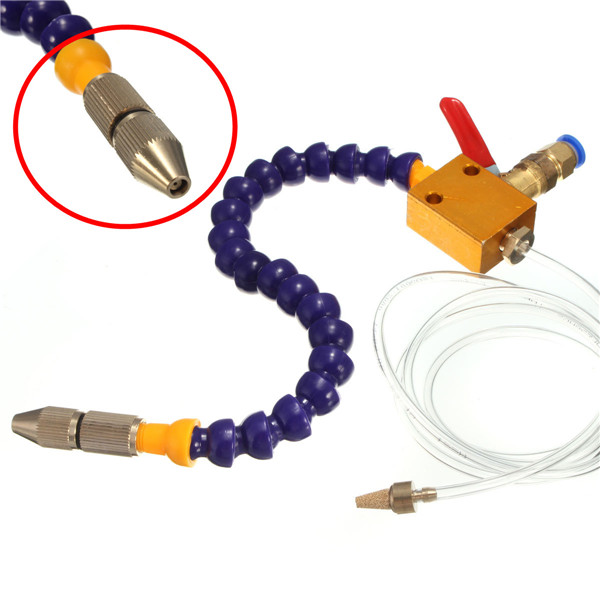
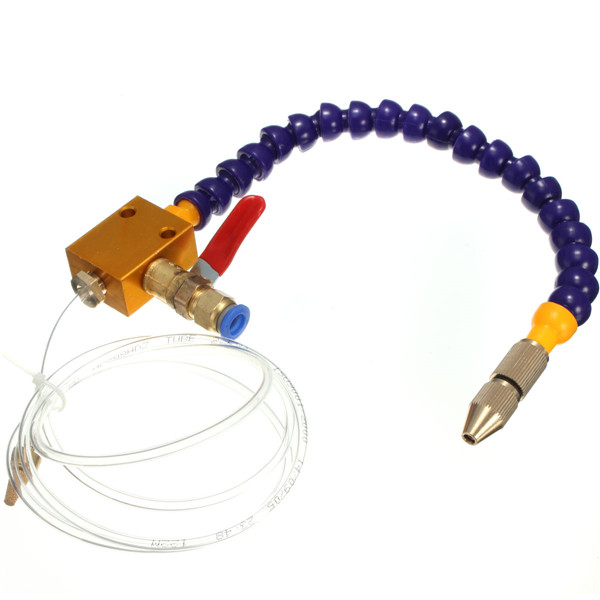
Spray for machine tools
Approx $30.74 USD
In the world of machinery, maintaining machine tools in top condition is essential for their longevity, efficiency, and smooth operation. One of the most effective ways to ensure your tools remain in peak condition is by using a high-quality spray for machine tools. These sprays are specifically formulated to lubricate, protect, and clean the various moving parts of machine tools, preventing wear and tear and enhancing performance. Whether you're in manufacturing, maintenance, or DIY, investing in the right machine tool spray can make a significant difference.
In this product description, we’ll discuss the importance of using a machine tool spray, its benefits, and how it can contribute to the overall performance of your machinery.
Key Features of Machine Tool Spray
1. High-Performance Lubrication
Machine tool sprays are designed to provide excellent lubrication to your machinery, ensuring that all parts run smoothly and without friction. Friction between moving parts can lead to wear and tear, causing premature failure of components and reducing efficiency. Using a lubricating spray helps to minimize friction, reduce heat buildup, and prevent the buildup of rust or corrosion.
These sprays are typically formulated to provide a long-lasting protective coating on machine surfaces, enabling smoother operations and extending the lifespan of parts such as gears, bearings, and other metal components.
2. Prevents Rust and Corrosion
One of the most common issues that machine tools face is rust and corrosion. Prolonged exposure to moisture, dust, and chemicals can lead to the deterioration of metal surfaces. A good machine tool spray will offer corrosion resistance, forming a protective barrier that shields metal components from rusting or corroding.
This is particularly important in environments where machine tools are exposed to harsh conditions, such as high humidity, frequent cleaning, or the use of aggressive chemicals. The protective layer prevents the oxidation process, which helps your tools last longer.
3. Cleans and Degreases
In addition to lubrication and corrosion protection, many machine tool sprays also feature cleaning and degreasing properties. Over time, machinery can accumulate dust, dirt, grease, and oil from regular use. This buildup can negatively affect the performance of the tools and even lead to overheating or malfunctioning.
A high-quality cleaning spray for machine tools can effectively remove this buildup, restoring the equipment to its optimal condition. By eliminating debris, grease, and oil, it ensures that the machinery operates efficiently, reducing the risk of jams and clogs.
4. Temperature Resistance
Machine tools often operate under high temperatures, especially when used for cutting, grinding, or heavy-duty operations. A machine tool spray formulated with temperature resistance ensures that it remains effective under these extreme conditions. Whether your machinery is exposed to high heat during manufacturing processes or used in precision tasks that require constant friction, a quality spray will continue to protect and lubricate, even at elevated temperatures.
The heat-resistant formula prevents the lubricant from breaking down or evaporating, ensuring long-lasting protection throughout the machine's operation.
5. Reduces Friction and Wear
Excessive friction can cause components to wear out quickly, leading to downtime, increased maintenance costs, and more frequent repairs. Using a machine tool spray reduces friction, allowing the parts to move smoothly without excessive contact. This helps to keep your tools running for longer periods with fewer mechanical issues.
By reducing friction, the spray also minimizes the amount of heat generated during operation, which can prevent overheating and extend the lifespan of your equipment.
6. Easy Application
A good spray for machine tools should be easy to apply, even in hard-to-reach areas. Most sprays come in aerosol cans, making it simple to target specific areas of the machine. Whether you need to lubricate gears, bearings, or rails, the spray nozzle provides precise application, minimizing waste and ensuring that you apply the right amount of lubricant where it's needed most.
Some sprays may also come with additional features, such as a straw nozzle for detailed application or a long-lasting formula that reduces the frequency of reapplication.
7. Safe for Different Materials
Machine tools are made of a variety of materials, such as steel, aluminum, and other metals. The machine tool spray you choose should be safe for use on these materials, ensuring that the lubrication, cleaning, and protection do not cause any damage or degradation to the tool surfaces.
Most high-quality sprays are formulated to be compatible with various materials, ensuring that they work across different types of machinery without compromising the quality of the tool surfaces.
Benefits of Using Machine Tool Spray
1. Enhanced Performance and Efficiency
By reducing friction and preventing rust, a machine tool spray improves the overall performance of your machinery. It ensures that the tools operate efficiently without the need for constant adjustments or repairs. This leads to better productivity and less downtime, which can significantly improve the output of your operations.
2. Prolonged Equipment Life
The lubrication and corrosion-resistant properties of the spray help to extend the life of your equipment. Regular use of a machine tool spray ensures that parts are protected from wear, reducing the need for replacements and maintenance. This can result in cost savings and increased equipment reliability over time.
3. Cost-Effective Maintenance Solution
Using a lubricant spray is a cost-effective solution for maintaining your machine tools. Instead of investing in costly repairs, replacements, or overhauls, regular use of a spray can help keep your machinery in optimal condition for longer, reducing the likelihood of expensive breakdowns and unnecessary repairs.
4. Versatility
Machine tool sprays are versatile and can be used for a wide range of applications. They are effective for a variety of tools, including cutting machines, drilling machines, lathes, milling machines, and other equipment commonly found in workshops and factories. Whether for metalworking, woodworking, or plastic processing, these sprays are designed to meet the demands of various industries.
5. Improved Safety
By reducing friction and preventing overheating, the machine tool spray helps to keep machinery running safely. It minimizes the chances of overheating or malfunctioning during operation, which can be a serious safety concern in manufacturing environments.
How to Use Machine Tool Spray Effectively
-
Clean the Machine Surface: Before applying the spray, ensure the surface of the machine is free from dirt, dust, and
debris. This ensures the spray can work effectively without any blockages.
-
Apply Evenly: Hold the can at a distance of 4-6 inches from the machine surface and spray evenly. Pay attention to areas
that experience high friction, such as gears, rails, and other moving parts.
-
Allow the Spray to Settle: Let the spray sit for a few moments, allowing it to penetrate and coat the surfaces effectively.
- Wipe Off Excess: If necessary, wipe off any excess spray to prevent buildup or mess around the machine.
- Regular Application: For maximum benefit, use the spray regularly, depending on how often the machine is used.
Description:
Etching machine spray cooling, special design, rotation direction, easy to use.
Standard fixture, thin nozzle and long service life.
specification:
Material: plastic, metal and brass
Dimensions: 36 cm (-L, approximately 1 m pipe)
Suitable for 8mm duct
Cooling stone / metal / tile etching machine
CNC lathe
feature:
Many tools to solve water problems are easier to clean.
The cooling liquid treatment can save more than 80%, and the cooling effect is not lower than conventional water cooling.
Insufflation processing chips make them work more safely.
The gas and coolant of the atomizer are adjustable and easy to use under different processing conditions.
Even the precision of high-temperature alloys machined from the workpiece can produce a smooth surface.
This not only increases the cutting speed, saves time, and reduces processing costs and tool wear.
The product may be provided by a different brand of comparable quality.
The actual product may vary slightly from the image shown.